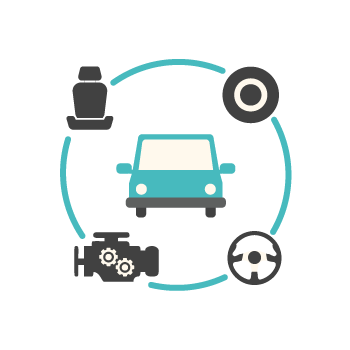
How cars are made

Upgrade for more content
Some car parts are big and heavy, and assembling them requires great accuracy. This work is often done by __________.
Jenny is helping her friend Aki to fix her car. There are so many different parts! How did anyone put this all together?! A very interesting question, Jenny! Let’s find out how cars are made!
A lot of thought goes into designing a car, long before it is made. A team of designers and engineers discuss and sketch ideas about the car’s looks and features. They develop a concept. Based on the concept, the development team creates models of the cars: virtual and physical. These models let them test the new car.
How will the different parts work together? How will the car hold up in a crash? Once the models have passed all the tests, production planning begins. The car company sources the steel, aluminium, rubber, glass, plastic, textiles — the raw materials — it will need to make the car. It plans which parts it will make itself, and which it will order from other companies — from suppliers.
Once the raw materials and parts are gathered, assembly can begin. In the past, a few well-trained craftsmen would assemble an entire car themselves, from start to finish. This took a long time, and it required each worker to have an extensive knowledge of the whole process. This made car production very slow and costly. Since then, cars have become much more advanced.
Production methods have changed too! Let’s see how this car is assembled, step by step. First, a metal frame is welded together. This will be the base of the car — the chassis. The chassis is placed on a conveyor belt and moves through a series of assembly stations.
Different workers install the engine, fuel tank, drive shafts, and gearbox onto the chassis. In another part of the factory, the car body is made. This starts with the largest component — the floor pan. As the floor pan moves down the different work stations, front and rear quarter panels, door pillars and side panels are attached. But this isn’t all done by workers.
Some of these components are big and heavy, and assembling them requires great accuracy. So, robots position the car parts and weld or bolt them into place. Once the main structure of the body is finished, robots and workers work together to install the doors, hood panel, trunk lid and other components. Next, the car body goes through a quality inspection. Any imperfections are found and repaired.
Now, the body can be painted. Layers of coatings and paint are applied in several rounds, with time to dry and cure in between. Next, interior elements are added: seats, radio, steering column, pedals… Lights and windows are added at this stage, too. The body is finally ready to be joined to the chassis. This operation is often controlled through a computer, to make sure that the body and chassis fit together perfectly.
Then, the car gets finishing touches: tyres, a charged battery, fuel... and it’s ready to roll by itself! After one last quality control inspection, the car leaves the factory, ready to be bought. Did you notice how the car moved from one workstation to another? The car was produced on an assembly line.
At each station, just a few specialised tasks were performed either by skilled workers or robots. Using assembly lines and automation, multiple cars can be manufactured simultaneously. This saves time and money. So many cars can be produced, fast! Thanks to this, cars have become so common we don’t often wonder anymore about how they are made.
But now, you can think about it, next time you get into a car. Or when you’re trying to fix one!