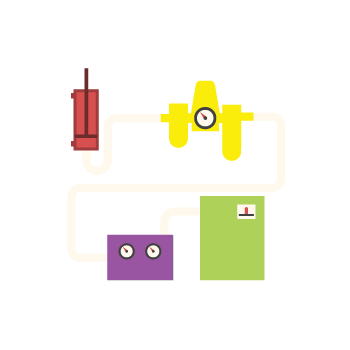
Pneumatics

Upgrade for more content
True or false? There are different types of actuators.
Michael and Leon are waiting for a bus. Here it comes! What was that sound?! What? That whizz and puff?
There, again! I don’t know. Maybe something on the bus is broken? That’s an interesting theory, but, in fact, this sound comes from the brakes of the bus. Because buses are large, heavy, and take many passengers aboard, their brakes must be powerful and reliable.
The braking systems of cars use hydraulic fluid, but this fluid might leak causing the braking system to malfunction. So instead, buses rely on a different system — air brakes. To make a bus come to a stop, air brakes use compressed air. When the bus driver brakes, air is let out of the system. And that’s why you hear a whizzing puff as the bus stops.
Air brakes are an example of a pneumatic system. Let’s see how pneumatic systems work! Take a balloon. Blow air into it. As you blow more air into the balloon, the air inside becomes compressed, and potential energy builds up.
Keep the balloon’s opening closed with your fingers. You’re storing the potential energy inside the balloon. Now, let go of the balloon. The compressed air gushes out. The potential energy turns into energy of motion, kinetic energy, causing the balloon to fly away.
Pneumatic systems make use of a compressed gas, usually air, to control and transmit energy, and to perform work. Pneumatic systems usually do this using five basic components. The first component, at the start of the system, sucks in the air from the atmosphere and compresses it. This is the air compressor. The air compressor can be powered by an electric motor or by a combustion engine, such as a diesel or petrol engine.
At the end of the pneumatic system there is a component that uses the compressed air to perform work, such as lifting, holding, or moving an object. This is the actuator. Depending on what the pneumatic system is used for, the actuator can be different. It can be a piston that moves back and forth in a straight line, or an air-motor, which makes things spin. The air compressor and the actuator need to be connected, so the air can flow between them.
This is done by a pipe, or a system of pipes, through which air can travel from the compressor to the actuator. This is the circuit of a pneumatic system. There is also a component that allows us to control the flow of the compressed air. It allows the actuator to be started or stopped at any time and the direction of motion to be reversed. This component is the valve.
The last basic element of a pneumatic system is an air tank, where a larger amount of compressed air is stored. With an air tank in place, there is always a reservoir of pressurised air that can be used, as soon as the valve is opened. Without an air tank, it would take very long for a compressor to build enough pressure to make the actuator move. Apart from air brakes on buses and other heavy vehicles, pneumatic systems have many applications in industry and our everyday lives. Pneumatic machines are used in factories to pick up, move, or place objects.
There are also tools that use pneumatic systems, like jack hammers for breaking up asphalt and pavement, nail guns, and even dental drills. And that’s our stop!